Fasteners and Machining: Necessary Components for Precision Manufacturing
Fasteners and Machining: Necessary Components for Precision Manufacturing
Blog Article
Introducing the Ins And Outs of Fasteners and Machining Processes for Optimum Efficiency
In the realm of engineering and production, the choice of fasteners and the details of machining procedures play an essential role in determining the ultimate efficiency and longevity of an item. From the relatively straightforward task of picking the ideal kind of fastener to the facility precision machining techniques utilized, every action in this process needs precise attention to information. As we embark on this expedition into the world of bolts and machining, we will reveal the subtle yet essential aspects that can substantially impact the effectiveness and top quality of the end product, clarifying the commonly overlooked elements that can make all the distinction in achieving optimum performance.
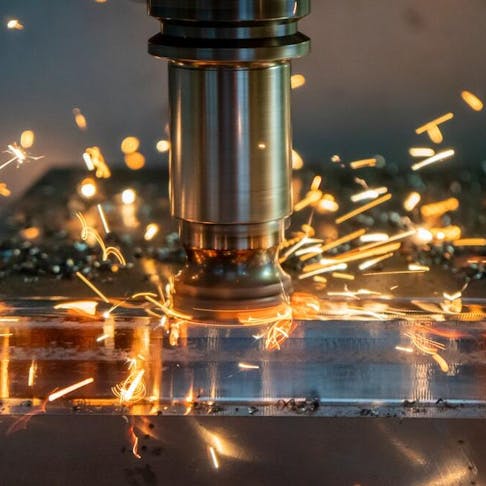
Value of Appropriate Fastener Choice
Choosing the suitable fasteners is crucial in making certain the architectural honesty and durability of any mechanical assembly. Bolts play a basic function in holding elements together firmly, with the ideal choice contributing considerably to the overall efficiency and dependability of the assembly. When picking fasteners, variables such as material compatibility, environmental problems, load-bearing capability, and simplicity of installation have to be carefully taken into consideration to ensure optimum performance.
Inappropriate fastener selection can bring about a variety of issues, consisting of loosening, deterioration, and even architectural failure. Making use of fasteners that are not matched to the specific needs of the assembly can endanger its functionality and posture safety threats. Engineers and designers need to meticulously examine the application requires and select bolts that fulfill or exceed the essential standards and specs.
In addition, the appropriate bolt selection process entails assessing the joint style, prepared for loads, vibration degrees, and potential thermal growth or tightening to make certain that the selected bolts can hold up against the operating conditions efficiently. By prioritizing appropriate bolt option, manufacturers can improve the top quality, sturdiness, and efficiency of their mechanical settings up.
Kinds and Features of Bolts
A vital element of mechanical settings up exists in understanding the diverse types and distinct attributes of bolts made use of in numerous commercial applications. Bolts are critical parts that hold frameworks with each other, ensuring stability and functionality. There is a large range of fasteners available, each designed for specific purposes based on the application needs. Common sorts of bolts consist of screws, screws, nuts, rivets, pins, and washers.
Screws are threaded bolts that are commonly made use of to sign up with two or even more elements together. Bolts are comparable to screws however are generally made use of with a nut to produce a secure joint. Nuts are inside threaded fasteners that mate with screws to hold elements with each other. Washers are thin plates that disperse the load of a bolt, preventing damages to the material being secured. Rivets are permanent bolts that are hammered or pressed right into place. Pins are utilized for alignment or to protect components briefly.
Understanding the attributes of each kind of bolt is necessary for picking the best one for a particular application, making sure optimal performance and dependability of the mechanical assembly. Fasteners and Machining.
Precision Machining Techniques for Efficiency
The detailed style requirements of numerous fasteners necessitate using precision machining techniques for ideal effectiveness in manufacturing procedures. One of the key methods used in accuracy machining is Computer Numerical Control (CNC) machining, which enables high degrees of accuracy and repeatability in the production of bolts.
Along with CNC machining, other accuracy techniques such as grinding, milling, and transforming are frequently used to attain the limited resistances required for bolts. These methods permit producers to develop fasteners with smooth surface areas, precise measurements, and high architectural stability. By making use of precision machining strategies, producers can boost the quality of bolts, reduce material waste, and boost overall manufacturing performance. Moreover, the use of innovative machining processes assists ensure that bolts meet market requirements and consumer expectations for efficiency and reliability.
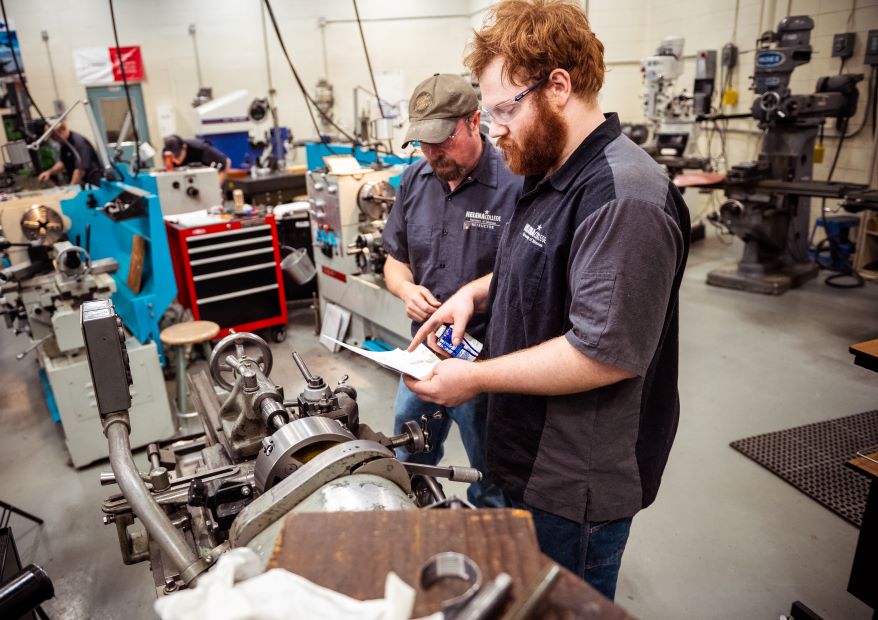
Variables Influencing Machining Refine Performance
Various variables play a considerable role in figuring out the performance of machining procedures in the production of fasteners. The initial crucial factor is the option of reducing devices. Picking the suitable devices based on the product being machined, desired surface, and reducing speeds can considerably impact the effectiveness and quality of the machining procedure. Furthermore, the find more information reducing parameters such as reducing rate, feed rate, and deepness of cut are essential variables that influence efficiency. Fasteners and Machining. Enhancing these parameters based on the certain requirements of the fastener being generated is vital to achieving accurate and cost-efficient machining.
Equipment rigidness and security also play an essential role in determining machining procedure efficiency. A well-informed operator can make real-time adjustments, troubleshoot concerns effectively, and make sure that the machining process runs smoothly, inevitably influencing the last high quality of the bolt.
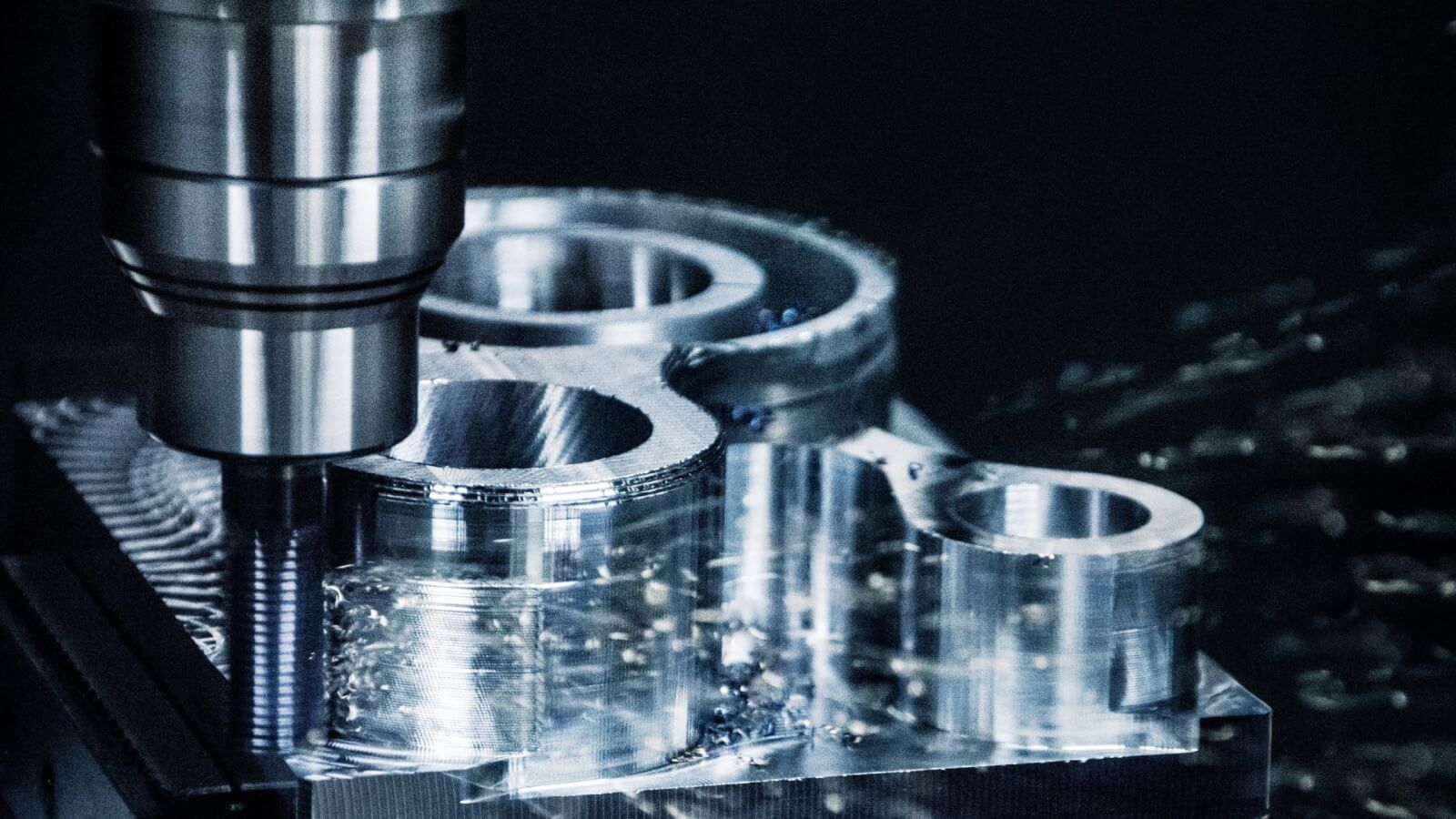
Quality Assurance Measures in Manufacturing
Variables influencing machining procedure efficiency, such as cutting device selection and maker security, directly effect the execution of quality control procedures in production. Regular maintenance Find Out More of machining devices is additionally important to maintain top quality control. By adhering to strict top quality control measures, producers can boost customer complete satisfaction, construct an online reputation for reliability, and eventually accomplish optimum efficiency in their machining processes.
Conclusion
To conclude, choosing the ideal bolts and utilizing precision machining methods are essential for ideal performance in producing procedures. Recognizing the types and qualities of fasteners, together with aspects influencing machining process performance, can result in enhanced effectiveness and quality assurance procedures. By focusing on these details, suppliers can attain greater degrees of performance and dependability in their products.
In the realm of engineering and manufacturing, the option of bolts and the ins and outs of machining processes play a critical role in determining the ultimate efficiency and longevity of an item (Fasteners and Machining). One of the main techniques click here for more used in accuracy machining is Computer Numerical Control (CNC) machining, which enables high degrees of precision and repeatability in the production of bolts. The usage of sophisticated machining processes helps make certain that bolts meet sector requirements and client expectations for efficiency and reliability
In conclusion, picking the best bolts and using precision machining strategies are vital for optimal efficiency in producing processes. Recognizing the types and characteristics of bolts, along with elements affecting machining process efficiency, can lead to enhanced performance and top quality control steps.
Report this page